公司简介
京电首研(天津)科技有限公司专注于变压器、电抗器及电源设备的研发与制造,以ISO 9001质量管理体系为基础,结合5S精益管理模式,建立标准化、柔性化制造流程,高效响应客户定制需求。
公司正从半无纸化向全面无纸化管理转型,依托电子文档系统及云端协同平台,实现技术图纸设计、工艺文件审批与数据归档全流程数字化,通过智能检索功能与权限分级管控机制,保障数据高效流转和安全可溯,为定制化产品开发提供精准技术支撑。
依托管理优化与技术创新的协同驱动,公司采用模块化设计架构与柔性产线布局,严格遵循品控标准,建立透明可追溯的交付流程,为客户提供高可靠性、定制型电力设备解决方案,推动能源行业向智能、可持续方向升级。
生产制造流程
京电首研(天津)科技有限公司将ERP系统深度嵌入变压器、电抗器等电力设备制造流程,打通订单、物料、生产、质检等环节数据链,构建标准化、可追溯的管控体系,并有专门的排单员统筹调度,确保资源高效配置与订单准时交付。
产品管控
——产品全生命周期管控:从设计到交付的精准护航
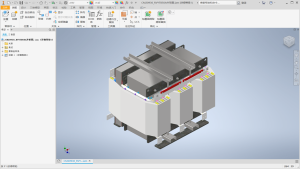
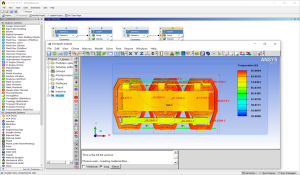
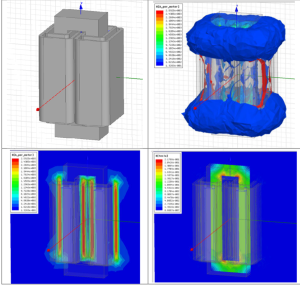
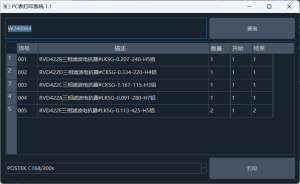
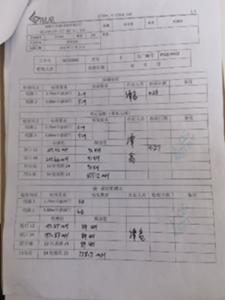
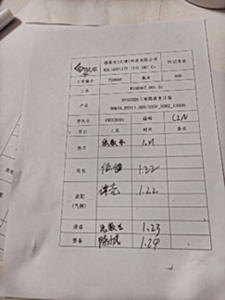
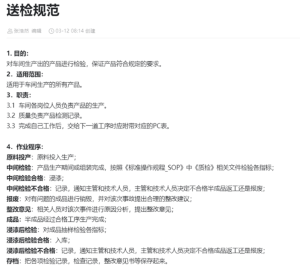
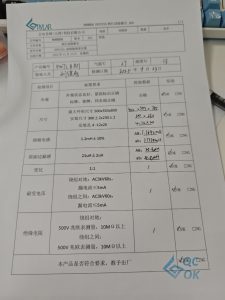
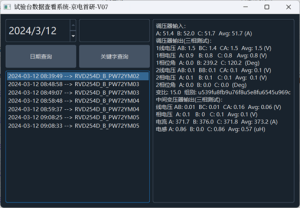
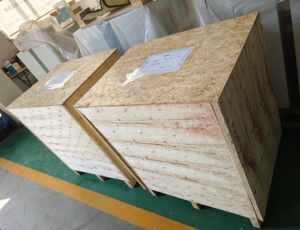
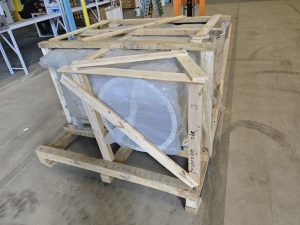
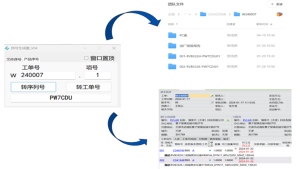
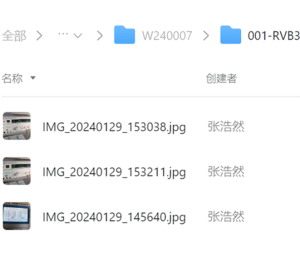
不良品处理
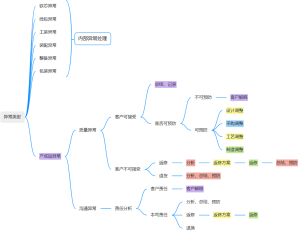
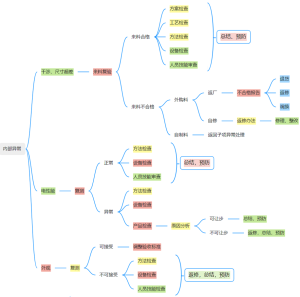
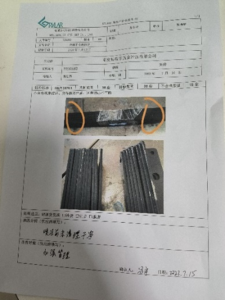

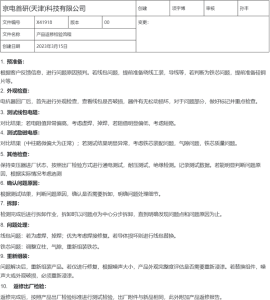

员工综合能力提升培训体系
公司建立涵盖SOP(标准作业程序)操作、工艺技术及安全防护的系统化培训机制,针对新老员工制定分层培养计划:新员工需通过岗前操作认证与安全实操培训,在岗人员定期参与工艺更新及风险防范能力训练。培训结合理论讲解、模拟操作与现场实践,辅以电子化学习档案跟踪进度,持续提升员工规范操作能力和安全意识,保障生产质量与作业安全。
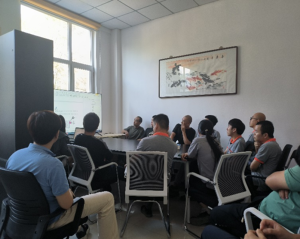
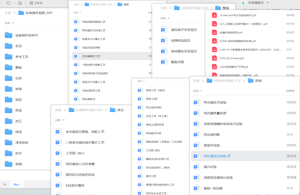
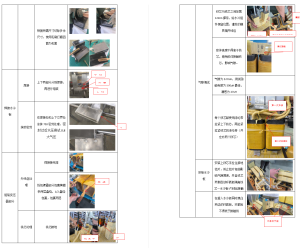
车间标准化管理成效说明
通过ISO 9001质量管理体系与5S现场管理标准的系统化结合,车间建立全流程规范管理机制:物料按定置图分类存放、区域标识清晰明确、工具工装定点定位;每日开展5S日常检查并纳入绩效考核,结合可视化看板实时追踪整改进度。管理体系的有效实施使车间环境持续保持整洁高效,设备利用率及物料周转效率显著提升,为产品质量与交付稳定性提供可靠保障。
以下为车间部分区域实拍图:
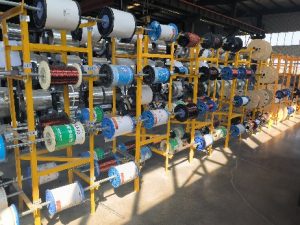
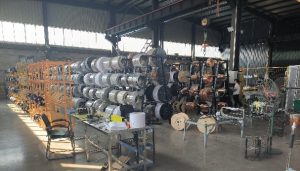
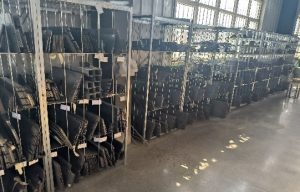
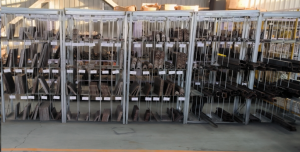
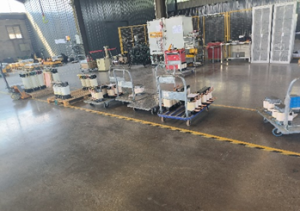
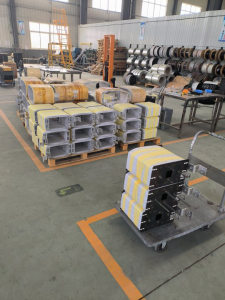
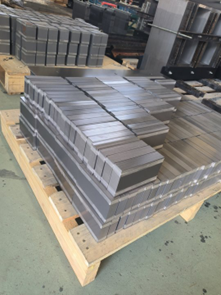
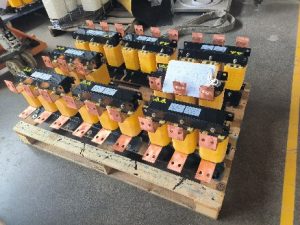
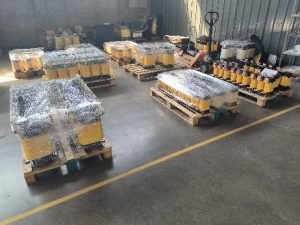
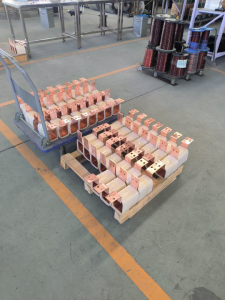
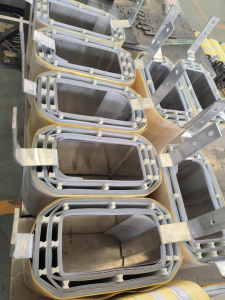
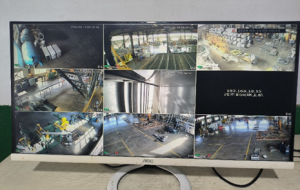